An Unbiased View of Alcast Company
An Unbiased View of Alcast Company
Table of ContentsGetting My Alcast Company To WorkNot known Facts About Alcast CompanyOur Alcast Company PDFsThe Definitive Guide to Alcast Company4 Simple Techniques For Alcast CompanyThe Greatest Guide To Alcast Company
The refined difference lies in the chemical web content. Chemical Contrast of Cast Aluminum Alloys Silicon promotes castability by decreasing the alloy's melting temperature and boosting fluidity during spreading. It plays a crucial duty in enabling intricate molds to be filled up precisely. Furthermore, silicon adds to the alloy's stamina and wear resistance, making it valuable in applications where durability is essential, such as auto components and engine components.It likewise enhances the machinability of the alloy, making it easier to refine right into completed items. In this means, iron adds to the overall workability of aluminum alloys.
Manganese contributes to the strength of aluminum alloys and boosts workability. Magnesium is a lightweight aspect that provides stamina and impact resistance to light weight aluminum alloys.
5 Easy Facts About Alcast Company Described
It allows the manufacturing of light-weight components with outstanding mechanical homes. Zinc improves the castability of light weight aluminum alloys and assists control the solidification process during casting. It boosts the alloy's strength and hardness. It is typically located in applications where intricate shapes and great information are required, such as decorative castings and certain automobile parts.
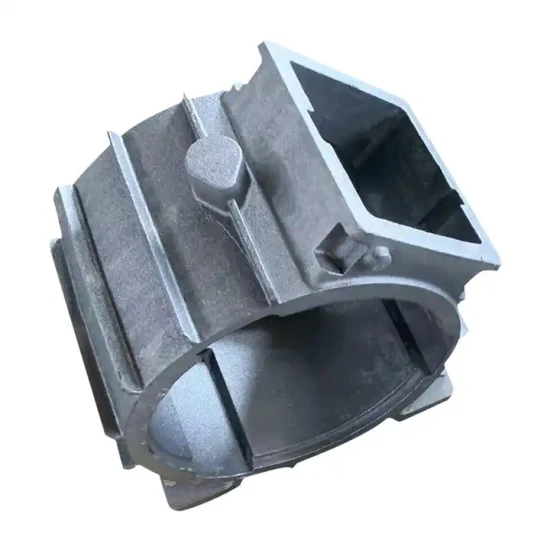
The key thermal conductivity, tensile strength, return toughness, and elongation vary. Select appropriate basic materials according to the performance of the target product produced. Among the above alloys, A356 has the highest thermal conductivity, and A380 and ADC12 have the least expensive. The tensile limit is the opposite. A360 has the best return stamina and the highest possible prolongation rate.
The Alcast Company Statements

In accuracy spreading, 6063 is fit for applications where detailed geometries and top notch surface area coatings are extremely important. Instances include telecommunication units, where the alloy's premium formability enables smooth and visually pleasing designs while maintaining architectural honesty. In a similar way, in the Illumination Solutions market, precision-cast 6063 elements create elegant and reliable illumination components that call for complex forms and good thermal efficiency.
It leads to a better surface area finish and better rust resistance in A360. The A360 exhibits premium elongation, making it perfect for complex and thin-walled parts. In precision spreading applications, A360 is appropriate for industries such as Customer Electronics, Telecommunication, and Power Devices. Its enhanced fluidness permits detailed, high-precision parts like smartphone coverings and communication gadget real estates.
5 Simple Techniques For Alcast Company
Its one-of-a-kind residential properties make A360 a useful selection for accuracy spreading in these markets, boosting item toughness and top quality. Light weight aluminum alloy 380, or A380, is a widely made use of casting alloy with numerous distinct characteristics. It offers excellent castability, making it an optimal option for precision casting. A380 exhibits good fluidness when molten, making certain detailed and detailed mold and mildews are precisely recreated.
In precision spreading, aluminum 413 beams in the Customer Electronic Devices and Power Equipment industries. It's commonly utilized to craft detailed elements like smart device real estates, electronic camera bodies, and power device cases. Its precision is impressive, with tight tolerances up to 0.01 mm, ensuring remarkable item setting up. This alloy's exceptional rust resistance makes it a superb selection for outdoor applications, making certain durable, sturdy items in the mentioned industries.
Examine This Report about Alcast Company
As soon as you have actually decided that the light weight aluminum die casting procedure Look At This is appropriate for your job, an essential following action is choosing the most ideal alloy. The light weight aluminum alloy you select will considerably affect both the casting process and the buildings of the end product. As a result of this, you should make your choice carefully and take an enlightened method.
Figuring out the most ideal aluminum alloy for your application will mean weighing a vast range of attributes. The initial group addresses alloy features that affect the manufacturing process.
An Unbiased View of Alcast Company
The alloy you select for die spreading straight influences a number of elements of the casting procedure, like exactly how simple the alloy is to deal with and if it is prone to casting flaws. Hot breaking, likewise called solidification cracking, is a typical die casting defect for aluminum alloys that can result in interior or surface-level splits or splits.
Specific aluminum alloys are a lot more at risk to hot breaking than others, and your selection needs to consider this. It can damage both the cast and the die, so you should look for alloys with high anti-soldering buildings.
Corrosion resistance, which is already a remarkable attribute of light weight aluminum, can vary significantly from alloy to alloy and is an essential characteristic to think about depending on the environmental conditions your item will be subjected to (Aluminum Castings). Use resistance is an additional building generally looked for in light weight aluminum products and can differentiate some alloys